- Corporate responsibility
- Technologies
- Sustainability
- Recycling
- Polyester renewal technology
- Plastics
- Packaging
- Innovation
- Climate
- Circular economy
- Carbon renewal technology
Defining the plastic waste problem
Imagine all the items you’ve bought, used and discarded in your lifetime. How much space would they take up? What about the items discarded by your neighbors, friends and family? From cars to toys to electronics, appliances, textiles, building materials, packaging, household goods and decorations, we buy, use and discard a lot of things — many made with plastic.
And because we can place them in a trash bin or drop them at a dump, and they seem to disappear, we might not give much thought to their journey after that. Unfortunately, most will end up in a landfill, doomed forever to be “trash” or “waste” — a concept that is foreign to the natural world. And humans make so much of this waste that we are running out of landfill space around the world.
What if we could turn our old, discarded, no-longer-useful plastic into new things?
We would reduce our strain on natural resources and avoid digging giant holes and using our land to bury waste. We would reduce pollution and chemicals leaching into local environments. We would reclaim and repurpose valuable materials and reduce our carbon footprint.
Reducing our waste in these ways would do us a lot of good.
But how?
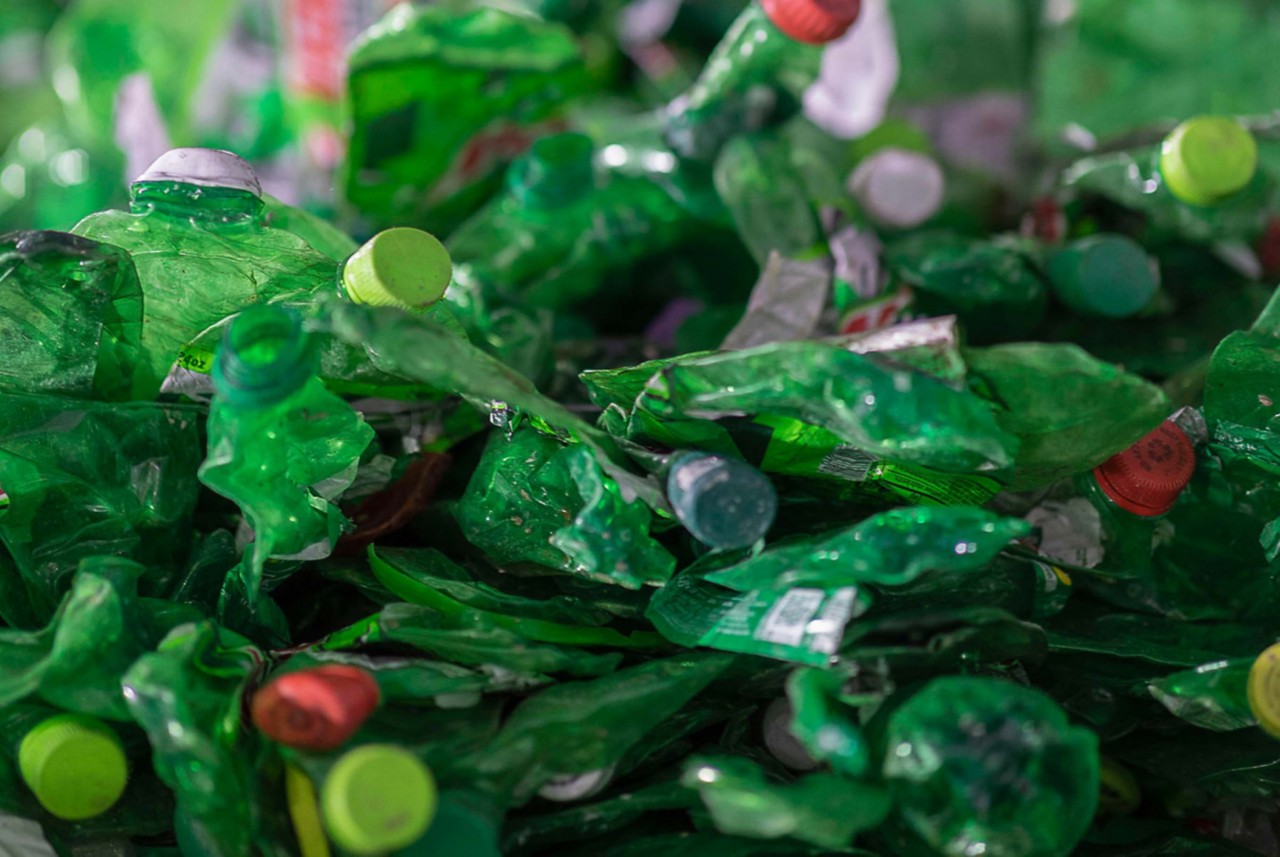
Our molecular recycling technologies allow us to recycle hard-to-recycle materials, such as colored PET.
The change needed for material circularity
To change our waste story, we need to adopt a circular mindset. Our perception of what end of life means for plastic needs to change. Instead of seeing the plastic we’ve used as mere waste, we should recognize its inherent value and reuse it accordingly. Molecular recycling technologies allow us to unlock this value.
The potential of molecular recycling of plastic is immense. By embracing it, we can reduce our dependency on fossil fuels, mitigate the prevalence of plastic waste in our environments and landfills, create value for end-of-life plastics, and transform existing plastic back into molecular building blocks for future products. This transition would create a circular economy, reducing our dependence on natural resources and minimizing our negative impact.
Right now, mechanical recycling is the dominant method for recycling plastic, but it’s limited to certain types of plastic. Others that aren’t recycled or landfilled may be burned for fuel. Mechanical recycling has the lowest carbon footprint and is the most cost-effective and efficient recycling option. Wherever possible, this is the best solution.
But mechanical recycling has limitations, starting with the very narrow range of simple plastics it can process, such as clear plastic water bottles and clear gallon milk jugs. Also, plastics that are mechanically recycled degrade each time they’re processed until they can’t be mechanically recycled anymore. Mechanical recycling is finite. Molecular recycling is infinite because the plastics do not degrade, no matter how many times they’re processed. And the vast types and amounts of plastic items that cannot be mechanically recycled — colored plastic bottles, eyeglass frames, food containers and polyester carpet are just a few — can be processed by molecular recycling.
To achieve true material circularity, we need material-to-material molecular recycling. To create a circular economy, we need to invest in better access, collection and sorting within the mechanical recycling system. We also need to build an infrastructure that supports molecular recycling to revolutionize materials.
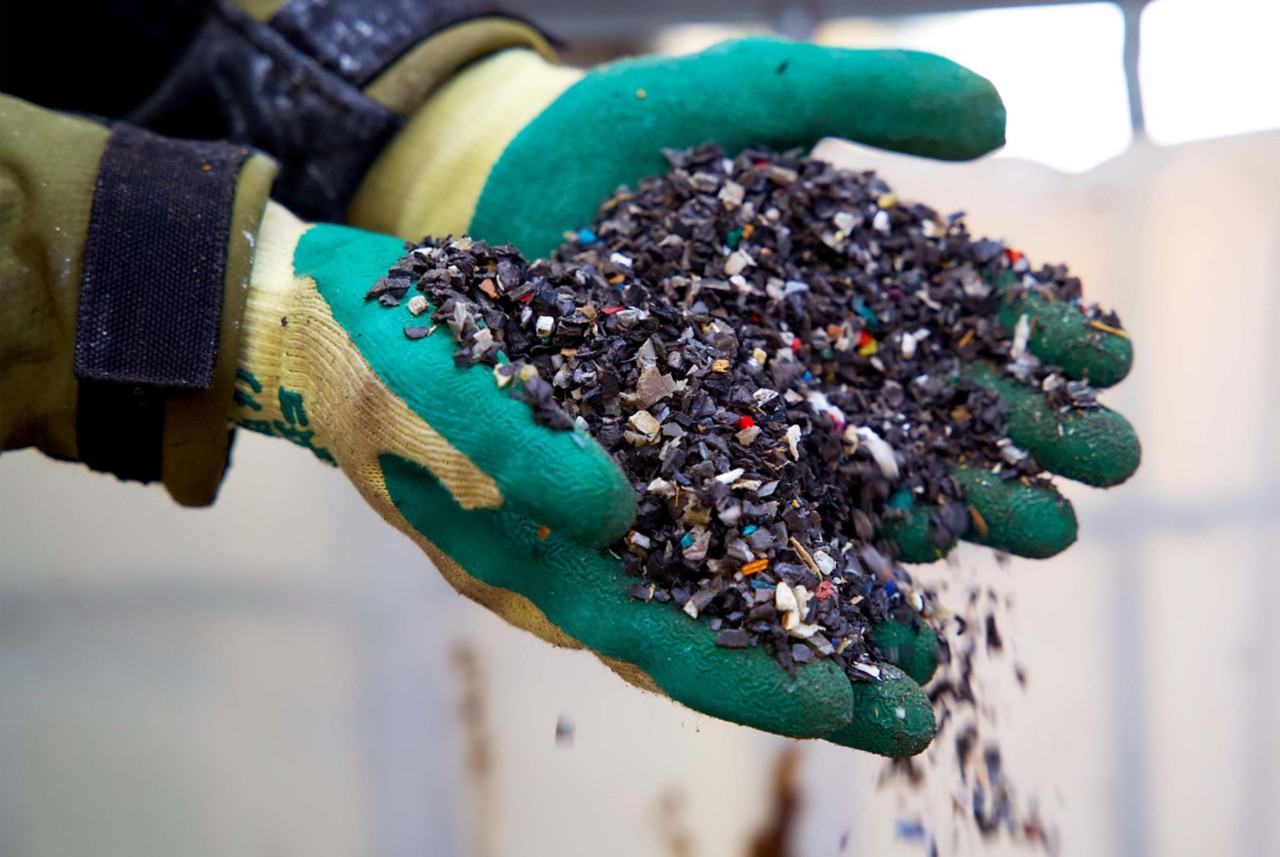
Automotive shredder residue (ASR) is another hard-to-recycle material from auto waste that we use in our molecular recycling technologies.
The complexity of advanced recycling
The phrase “advanced recycling” doesn’t really tell us much about the process. The general term covers any technology that transforms waste to be used again and isn’t traditional mechanical recycling. Technologies that some characterize as advanced recycling might in fact be transforming waste materials into fuel. We would argue that these technologies should not be characterized as recycling.
However, there are other technologies that are truly circular and produce building blocks identical to those produced from fossil resources, so they can then be used to make new high-performance materials. This is referred to as material-to-material recycling and is preferred. It keeps existing materials in use, reducing our need to create more from fossil resources. It’s also what we mean when we refer to Eastman molecular recycling.
But even within material-to-material molecular recycling, there are a range of technologies with varying environmental benefits or consequences. The most sustainable processes can repurpose an extremely high percentage of the processed waste with very little yield loss. They use the least amount of hazardous chemicals and have lower carbon emissions while producing useful feedstock from waste.
We know consumers are looking for recycled content. And that means businesses are looking for recycled materials. So why aren’t we doing more material-to-material molecular recycling?
The problem is most of these recycling technologies are relatively new. Recycling technologies and facilities are expensive and take time to build. With failing perception of recycling and confusion around accepted materials, more and more people are giving up on putting plastic in their recycling bins. Mechanical recycling, which our current infrastructure is built for, accepts limited types of plastics. And the range of accepted plastics varies by municipality.
One advantage of Eastman molecular recycling is that it recycles a wide range of materials that cannot be mechanically recycled. These technologies provide a means to recycle not just more plastic but more types of plastic — meaning less ends up in landfills.
This is the promise of molecular recycling. The challenge is that we don’t have a clear and consistent approach to collecting and recycling more plastics. To activate material circularity through molecular recycling, we need to aggressively pursue:
Design for recyclability
Improved access to recycling for a majority of households
Infrastructure for collecting and sorting waste and transporting it to proper recycling facilities
Molecular recycling facilities that operate at scale
Policies that enable the development of effective recycling technologies
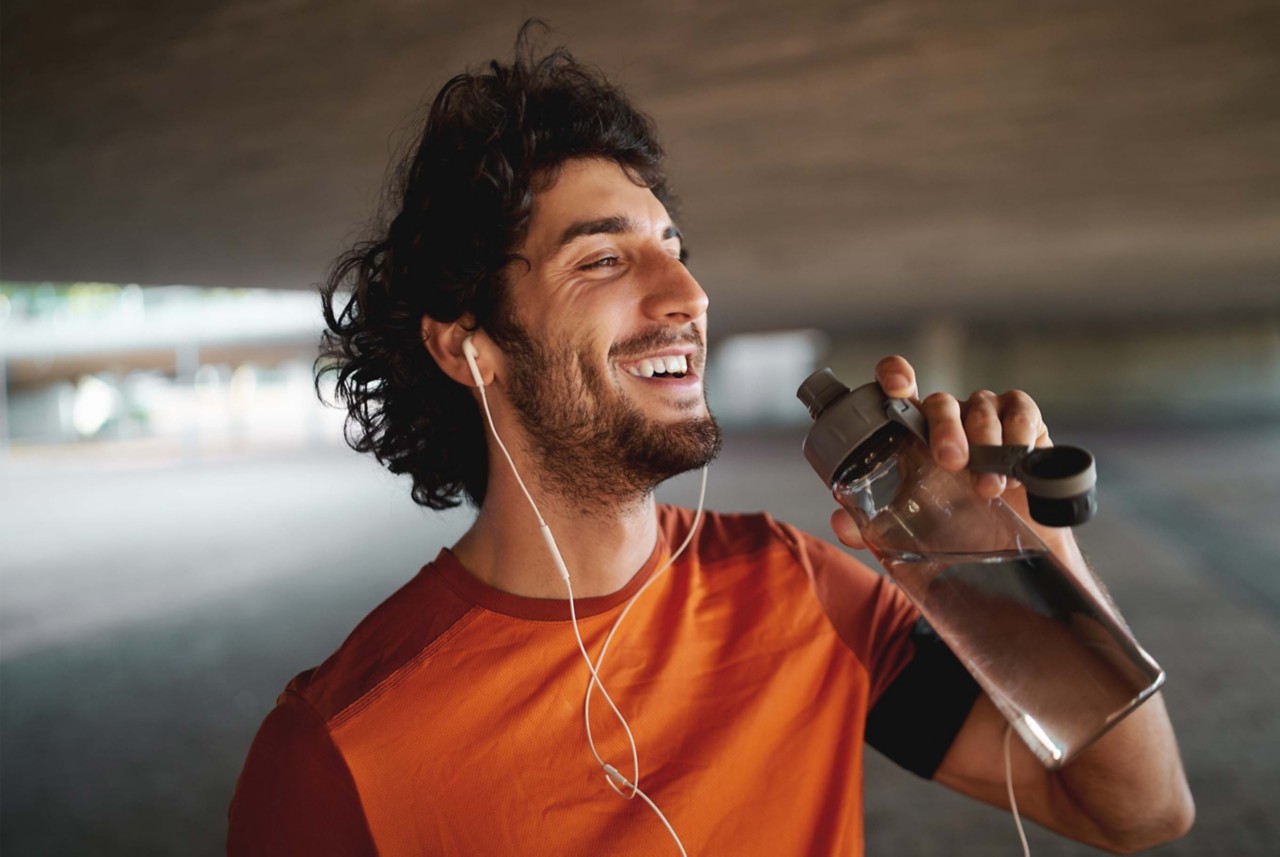
Eastman Renew materials are used to make durable goods like reusable water bottles.
What’s Eastman doing for a circular economy?
We’re working closely with waste management companies to create new feedstock streams. We’re also supporting take-back programs and collection efforts. That includes The Recycling Partnership’s PET Recycling Coalition, which offers grants to fund viable research, infrastructure and knowledge sharing to help capture more PET waste for recycling. We’re engaging in meaningful partnerships that are critical for scaling the circular economy.
Beyond that, we’re making significant investments in facilities that can implement molecular recycling and turn hard-to-recycle plastic waste into feedstock for new materials and products.
We’ve developed two technologies that can greatly expand plastic recycling: polyester renewal technology (PRT) and carbon renewal technology (CRT). These technologies complement mechanical recycling by accepting a wider range of plastics like those prevalent in plastic packaging, other single-use plastics, textiles and more. Our PRT facility in Kingsport, Tennessee, is nearing completion, and we’re targeting the facility to be operational by the end of 2023. It will be one of the largest material-to-material recycling facilities in the world, processing 110,000 metric tonnes of polyester waste annually and producing high-quality, new products that perform just like virgin materials.
We’ve also announced a similar PRT recycling facility in France. A partnership with Interzero will supply 20,000 metric tonnes of plastic waste to our facility to be turned into first-quality feedstock. When operational (expected by 2026), the first phase of the facility will be able to recycle 110,000 metric tonnes annually, with that growing to over 200,000 metric tonnes with the completion of the second phase.
With many companies looking for recycled content, these innovative and invaluable technologies can turn would-be waste into valuable materials and drive the circular economy forward.
A circular economy not only supports a more responsible approach to materials and business but also has countless positive impacts for society. Keep reading to learn how molecular recycling contributes to a circular economy and how circularity can improve the quality of life for billions around the world.